What's Inside |
Why Pre-Work Risk Assessments Matter
In the high-stakes world of construction, hazards are everywhere and pre-work risk assessments are crucial for preventing accidents and injuries. These evaluations help teams spot potential dangers, put controls in place, and ensure that every worker gets home safely at the end of the day.
However, despite the benefits, getting team members to fully embrace these assessments can be challenging. From experienced workers who think they've "seen it all" to new hires eager to prove themselves, resistance and skepticism can undermine safety efforts.
Conducting effective pre-work risk assessments requires more than just a checklist. It needs a shift in mindset, a shared commitment to safety, and a focus on the well-being of everyone on the team. It also requires understanding why people resist change and how to motivate them to adopt new behaviors.
Exploring common psychological barriers like complacency, overconfidence and time pressure can help you avoid a dangerous “it won’t happen to me” mentality.
These insights can then be used to form practical strategies that are effective in the real world. Creating a culture of safety and getting your team on board with pre-work risk assessments begins with understanding them.
You can then make these assessments part of the daily routine for safety managers, site supervisors and frontline workers alike. After all, when it comes to safety, the stakes in construction couldn’t be higher.
What are Pre-Work Risk Assessments?
Pre-work risk assessments are how you identify, analyze, and control potential hazards before construction work begins. These assessments, which may also be referred to as job hazard analysis’ (JHA), pre-task plans (PTP), construction risk assessments or pre-construction risk assessments (PCRA), are crucial for ensuring the safety of workers, site visitors, and building occupants. They are particularly important in sensitive environments such as hospitals, clinics, and healthcare facilities.
The main objectives of pre-work risk assessments include:
-
Identifying hazards: Recognizing potential dangers on the site before and during construction.
-
Assessing risks: Evaluating the likelihood and potential consequences of identified hazards.
-
Determining control measures: Establishing how to minimize or eliminate the identified risks. For example, implementing safety protocols, providing personal protective equipment (PPE), or modifying work procedures.
-
Ensuring compliance: Meeting legal and regulatory requirements
-
Raising awareness: Communicating potential risks to all stakeholders, including workers, supervisors, and site visitors, to foster a culture of safety and shared responsibility.
A comprehensive pre-work risk assessment should include the following key components:
1. A detailed description of the project scope and potential risks
2. An analysis of the areas surrounding the project that could be impacted
3. A list of specific construction activities and their hazards
4. Documentation of steps taken to mitigate risks
5. Completion of an interim life safety measures (ILSM) assessment and selection of appropriate safety measures
6. Ongoing monitoring to ensure the continued use of appropriate safety measures
In the construction industry, various terms are used interchangeably to describe these risk assessment tools, leading to some confusion. To clarify the differences and North America terminology, we have created a table that outlines the purpose, scope, timing, and regions where each term is commonly used. This table aims to help you understand and communicate effectively about these critical safety tools across different contexts.
Tool | Purpose | Scope | Timing | Regions Known |
Job Hazard Analysis (JHA) | Defined by OSHA. Identify and assess potential hazards for a scope of work | Broad, covering multiple tasks or the entire job | Before project begins or new job is introduced | US, Canada |
Pre-Task Plan (PTP) | Detailed, task-specific plan focusing on hazards, controls, and execution. Pulls information from a JHA | Specific to a particular task or activity | Daily or before specific tasks | US, Canada |
Job Safety Analysis (JSA) | Another term for Job Hazard Analysis | Same as JHA | Same as JHA | US, Canada |
Activity Hazard Analysis (AHA) | Similar to a Job Hazard Analysis with risk classification emphasis and used in the field daily by Army Corp of Engineers | Same as JHA - used by Army Corp of Engineers | Same as JHA - used by Army Corp of Engineers | US only |
Morning Huddle | Brief meeting to discuss tasks, hazards, and safety measures for the day | Daily, covering tasks and hazards for the day | Daily, before work begins | US, Canada, UK |
By understanding the different names and purposes of these tools, safety managers can better communicate and implement them, ensuring a safer work environment for everyone. Learn more about the difference between a JHA and PTP.
The Psychology of Resistance
While the benefits of pre-work risk assessments are clear, getting team members to fully embrace them can be challenging. Various psychological factors can contribute to resistance, creating barriers that safety managers need to understand and address.
One common hurdle is complacency. When workers get comfortable with routine tasks, they may start to believe that accidents won't happen to them.
This false sense of security can lead to a dangerous "it won't happen to me" mentality, causing workers to take shortcuts or ignore safety protocols [2].
Experienced workers might also become overconfident and feel that their years on the job make them immune to accidents. One article notes, "People with years of experience at a job are certainly very familiar with their job; they could 'do it with their eyes shut'. It is this familiarity with the job and all it entails that cause less stringent adherence to safety rules, becoming a dangerous problem" [3].
This overconfidence can cause workers to disregard safety procedures, leading to preventable injuries [3].
Time pressure is a third factor. When workers feel pressured to meet tight deadlines, they may be more likely to cut corners or take risks. As Nepal et al. explain, "Workers who perceive they have to overcome schedule pressure will tend to cut corners, even safety corners, in order to meet the schedule" [4].
This pressure can lead to mistakes that compromise safety.
Together, complacency, overconfidence, and time pressure can create strong resistance to pre-work risk assessments.
Overcoming this requires an approach that addresses each factor. Continuous learning, regular safety training refreshers, and involving workers in the risk assessment process are three ways in which safety managers can help break down these barriers and create a shared commitment to safety [1, 3].
Understanding Motivation and Behavior Change
Self-Determination Theory (SDT) suggests that people are more likely to engage in a behavior when they feel that it aligns with their values and goals, rather than being forced upon them by others [5].
In other words, workers will be more motivated to participate if they understand and value pre-work risk assessments as a way to protect themselves and their colleagues.
Safety managers can tap into this by involving workers in in the risk assessment process and giving them a sense of ownership.
By seeking peoples’ input and feedback, managers can create a shared sense of purpose around safety, rather than imposing a top-down mandate.
The Theory of Planned Behavior (TPB) shows how workers are more likely to embrace pre-work risk assessments if they believe that:
-
The assessments are valuable and effective
-
Their peers and supervisors expect and support participation
-
They have the knowledge, skills, and resources to conduct the assessments properly [6]
Safety managers can promote this by providing regular training and education to highlight the benefits of risk assessments.
The aim is to create a team culture that prioritizes safety and ensures workers have the tools and support they need to conduct assessments confidently.
Ultimately, you can create a safer environment when safety is seen as a shared value rather than a bureaucratic burden.
By understanding what motivates people and tapping into that, safety managers can turn resistance into commitment and build a safer workplace for all.
Strategies for Gaining Team Buy-In
So, if compliance can’t be demanded, what strategies can managers use to get team buy-in for pre-work risk assessments?
A key step is effectively communicating the value of these assessments through real life examples and success stories. If you can make the benefits feel real and relatable, people are more likely to take up the challenge.
It’s also crucial that supervisors and managers actively take part and prioritize safety in their decision-making.
Doing so will show workers that you are committed, and that safety is a non-negotiable part of the job. On the other hand, if leadership doesn’t take it seriously it can undermine safety and lead to accidents and greater risks.
Strategies you can use to create a productive, safety-first workplace include:
-
Seek input from workers to gain firsthand knowledge of job site hazards and practical challenges.
-
Provide regular training and refresher courses so workers have the right skills and knowledge.
-
Recognize and reward workers who consistently take the right approach to safety.
-
Encourage communication and feedback about safety concerns and suggestions for improvement.
-
Make risk assessments part of the daily routine.
Case Studies and Examples
While theories and strategies provide a solid foundation for implementing pre-work risk assessments, it's also valuable to learn from successful real-world experiences.
Case Study 1:
A large construction firm recognized the need to improve its safety performance after experiencing a series of near-misses and minor incidents. The company's leadership team realized that a reactive approach to safety was no longer sufficient and a proactive, risk-based approach was needed [2].
To achieve this, the company implemented a comprehensive pre-work risk assessment program that involved all levels of the organization, from frontline workers to senior management. The program included regular training sessions, a standardized risk assessment process, and a system for tracking and analyzing risk data over time [7].
Lessons Learned:
One of the key lessons learned from this experience was the importance of involving workers in the development and implementation of the risk assessment process. By seeking input and feedback from frontline teams, the company was able to create a system that was practical, efficient, and well-suited to the unique needs of each job site [5].
Case Study 2:
Another example comes from a midsize construction company that had struggled with inconsistent safety practices across its projects. To address this issue, the company implemented a peer-to-peer risk assessment program, where workers were trained to conduct assessments for each other before starting high-risk tasks [3].
Lessons Learned:
This approach helped to identify and mitigate risks more effectively by promoting teamwork and shared responsibility for safety. Workers began to look out for each other and hold each other accountable for following proper safety procedures [1].
While there is no one-size-fits-all approach to implementing pre-work risk assessments, there are common themes that contribute to success. These include leadership commitment, worker engagement, regular training, and a focus on continuous improvement [4].
Free Download - Pre-Work Risk Assessment
Designed by certified safety professionals
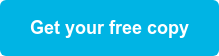
The Path Forward: Commitment to Safety
Understanding human factors is the key to creating a better safety culture. By doing so, you can get team buy-in and implement self-reinforcing safety behaviors that will reduce risks and, ultimately, save lives.
While there is no on-size-fits all solution, pre-work risk assessments are a great first step to embed safety into your company at all levels. To see how HammerTech can help you implement these assessments and enhance your safety protocols, request a demo today.
References:
[1] Complacency Kills: The Dangers of Complacency in the Workplace. (n.d.). OSHA.com Blog. https://www.osha.com/blog/complacency-safety
[2] Furst, P. (2017, April 28). Managing Complacency in Construction. IRMI.com. https://www.irmi.com/articles/expert-commentary/managing-complacency-in-construction
[3] Tool Box Talk: Overconfidence and Safety. (n.d.). Cornett's Corner. https://cornettscorner.com/tool-box-talk-overconfidence-and-safety/
[4] Leemann, J. E. (2016, March 1). Deadlines can erode safety and promote risk-taking. ISHN.com. https://www.ishn.com/articles/103452-deadlines-can-erode-safety-and-promote-risk-taking
[5] Ryan, R. M., & Deci, E. L. (2000). Self-determination theory and the facilitation of intrinsic motivation, social development, and well-being. American Psychologist, 55(1), 68-78. https://selfdeterminationtheory.org/theory/
[6] Bosnjak, M., Ajzen, I., & Schmidt, P. (2020). The theory of planned behavior: Selected recent advances and applications. Europe's Journal of Psychology, 16(3), 352-356. https://doi.org/10.5964/ejop.v16i3.3107
[7] Understanding Risk Management and Assessment. (2019, February 12). ASSP. https://www.assp.org/news-and-articles/conducting-a-risk-assessment