Job Hazard Analysis (JHA)
Learn how a Job Hazard Analysis (JHA) protects construction teams and enhances site safety.
Why Use a Job Hazard Analysis?

Reduce Risks
Identify and control potential hazards to prevent accidents and injuries, ensuring a safer work environment.

Ensure Compliance
Meet OSHA standards while reducing liability and avoiding penalties during inspections or audits.
.png)
Boost Efficiency
Integrate hazard controls into workflows to reduce delays, improve collaboration, and enhance safety.
Watch: How to Complete a Job Hazard Analysis (JHA) & Why It Matters
In this video, you'll learn:
-
Why JHAs are critical for safety and efficiency on every jobsite
-
How to break down tasks and identify hazards before work begins
-
Step-by-step guidance for completing the free JHA template
Download the JHA template and start improving safety today.
FAQs: Job Hazard Analysis (JHA)
A Job Hazard Analysis (JHA) is a structured process that helps identify and control potential hazards associated with specific job tasks. It is a key tool for improving safety and integrating health practices into daily operations on construction sites and beyond.
A JHA aims to:
- Identify hazards that could cause injury, illness, or property damage.
- Develop safe work procedures to eliminate or mitigate these risks.
- Train employees on how to perform tasks safely and effectively.
- Promote a culture of safety and compliance with regulations like OSHA.
Taken from the Comprehensive JHA Guide.
To conduct a JHA, general contractors should ensure subcontractors follow a systematic process. JHA expectations should be included in pre-work safety orientations and even in contractual agreements. OSHA’s JHA template is a good place to start in setting up a standard procedure. Here are the steps involved in completing JHAs:
1. Choose the job or task to be analyzed:
-
Consider selecting jobs or tasks that have a high risk of injury or illness, or those with a history of accidents or incidents. JHAs are also helpful before a new scope of work begins or a new piece of major equipment arrives onsite.
-
Take into account the level of complexity and the number of steps involved in the job or task.
2. Break the job or task down into steps:
-
Break down the job or task into individual steps or tasks to ensure that all hazards are identified.
-
Record each step or task on the JHA form or template.
3. Identify potential hazards:
-
Identify potential hazards associated with each step or task by considering past accidents, incidents, or near misses.
-
Consider potential hazards related to the equipment, tools, materials, and environment. Use not only the experience of your team to determine hazards but also read product information and safety data sheets (SDS).
4. Determine the severity and likelihood of each hazard:
-
Evaluate the severity and likelihood of each hazard to determine the overall risk level.
-
Use a risk matrix or other risk assessment tool to help prioritize hazards based on severity and likelihood.
5. Identify controls for each hazard:
-
Identify controls for each hazard that will eliminate or reduce the risk level to an acceptable level.
-
Consider using the hierarchy of controls, which prioritizes elimination or substitution, followed by engineering, administrative, and personal protective equipment controls.
6. Submit for approval before starting work:
-
A representative from the general contractor reviews the JHA and provides comments or accepts the subcontractor’s proposals to ensure it is site-specific and supports your safety standards.
7. Implement controls:
-
Use the JHA as the source of truth for work method and implement the identified controls for each hazard, making sure they are effective and feasible.
-
Ensure that workers are trained on the proper use of controls and that the controls are maintained and inspected regularly.
8. Review and update the JHA:
-
Regularly review and update the JHA to ensure that it remains current and effective.
-
Consider reviewing the JHA whenever there are changes to the job or task, equipment, or work environment, or when incidents or accidents occur, and make sure that workers are aware of the changes.
A JHA should be conducted for any task or activity with potential safety risks, especially:
-
Jobs with high incident or injury rates.
-
Tasks involving new equipment, processes, or procedures.
-
Activities where simple errors could lead to severe injuries.
-
Situations where past incidents have revealed unaddressed hazards.
-
Jobs complex enough to require written instructions.
Using a JHA offers significant advantages:
-
Reduces worker injuries and illnesses.
-
Promotes safer and more efficient work practices.
-
Helps maintain OSHA compliance and avoid penalties.
-
Lowers workers’ compensation claims and related costs.
-
Boosts employee morale and productivity.
Get Essential downloadable PDF Safety Templates
Access 7 expert-designed templates to improve your safety and compliance processes

Level up your safety game
Additional Resources
%20-%20Additional%20Resources%20image.png)
A Comprehensive Guide to Job Hazard Analysis’ in Construction: Tips and Tools for Success
6-Minute Read
Learn best practices for JHAs in this guide, including why they are crucial for construction, how they can help promote safety onsite, a...
Get Expert Insights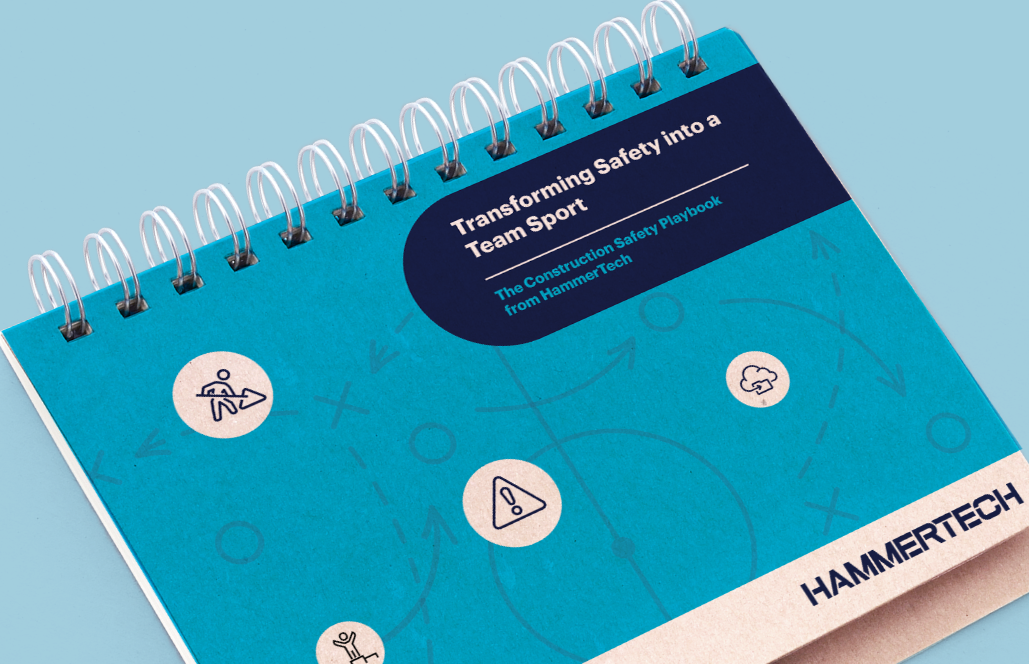
The Construction Safety Playbook: Standardize Safety & Improve Accountability
25-Minute Read
Create a safer, more consistent jobsite with structured safety processes and clear accountability. This expert-backed playbook provides...
Get The Playbook
The Psychology of Pre-Work Risk Assessments: How to Get Your Team on Board
9-Minute Read
In the high-stakes world of construction, hazards are everywhere and pre-work risk assessments are crucial for preventing accidents and ...
Dive in